The incident arose during the repair of a valve connected to a 12-inch pipeline that ran from the auxiliary boiler in the engine room to the main deck, used for heating the cargo warming coils. The repair was initiated after condensation was observed, leading the Chief Officer to suspect a faulty valve, even though the valve and heating system were not routinely used.
The Chief Engineer assigned the Second Engineer to carry out the repair. At approximately 10:00 AM, the Second Engineer conducted a toolbox meeting with the involved crew, detailing the steps: shutting down the auxiliary boiler, draining the pipeline of water, and blanking the line at a
flange near the boiler before commencing any work on the valve. During this meeting, the Fitter and the Motorman expressed concerns that this was a non-routine task more suitable for dry-dock conditions, but their objections were overruled and the job proceeded as planned.
The boiler was shut down, the line drained, and the blank installed before the crew took a lunch break. After lunch, the Fitter and Motorman positioned themselves beneath the valve to remove its bonnet cover. They had removed two nuts and partially loosened two others when a sudden
discharge of hot water—estimated between twenty and thirty litres—occurred. Because the workspace beneath the valve was confined to about one meter in width, the two men could not evade the surge of water. Both sustained burns to their legs, arms, back, buttocks, and portions of their faces. Although two other crew members in the vicinity received minor splashes and were treated with first aid onboard, the injuries to the Fitter and Motorman were more severe.
The Master arranged for the immediate evacuation of the injured men from the anchorage. They were transferred by launch from the vessel to shore and then taken to a specialized burn treatment facility at a local hospital. The following day a Marine Investigator and a legal
representative, along with three port state inspectors, boarded the vessel to investigate. During interviews with the Master, Chief Engineer, and involved crew, it emerged that there was no written procedure in the vessel’s Safety Management System (SMS) for this kind of maintenance.
Both the Master and Chief Engineer acknowledged the lack of formal guidelines and agreed that, going forward, more extensive personal protective equipment would be employed and additional cooling times instituted before undertaking similar work.
The Port State Inspector’s examination of the site revealed that caution tape now marked the valve area. They concluded their onboard inquiry and recommended prompt valve repair. Medical personnel indicated that while both crew members suffered first- and second-degree burns over a significant portion of their bodies, the burns were not deep, and treatment prognosis was favourable. They should be able to return to work.
Questions
When discussing this case please consider that the
actions taken at the time made sense for all involved. Do
not only judge but also ask why you think these actions
were taken and could this happen on your vessel?
- Does our SMS address these risks?
- What sections of our SMS would have been
breached if any? - How can we improve our toolbox meetings and
communication so that crew members feel
comfortable raising concerns, especially for nonroutine
jobs? - What additional steps can we take to ensure that
equipment is fully cooled, isolated, and safe to
work on before maintenance begins? - In what ways can we enhance our PPE standards
to match the specific hazards of each task, such
as working with hot fluids under pressure?
- How can we ensure that all crew members,
including engineers and deck crew, receive
continuous training on hazard recognition, risk
assessment, and proper emergency response? - What communication channels can we
strengthen to make certain that safety concerns
raised during toolbox meetings are properly
evaluated and escalated if necessary? - How should we follow up after an incident to
confirm that corrective actions (such as updated
procedures, improved PPE, and training) have
been implemented and are effective? - How can we encourage a proactive safety culture
where lessons learned from past incidents—both
onboard and from industry sources—are regularly
reviewed, discussed, and incorporated into daily
operations? - What immediate, actionable steps can we take
from today’s discussion?
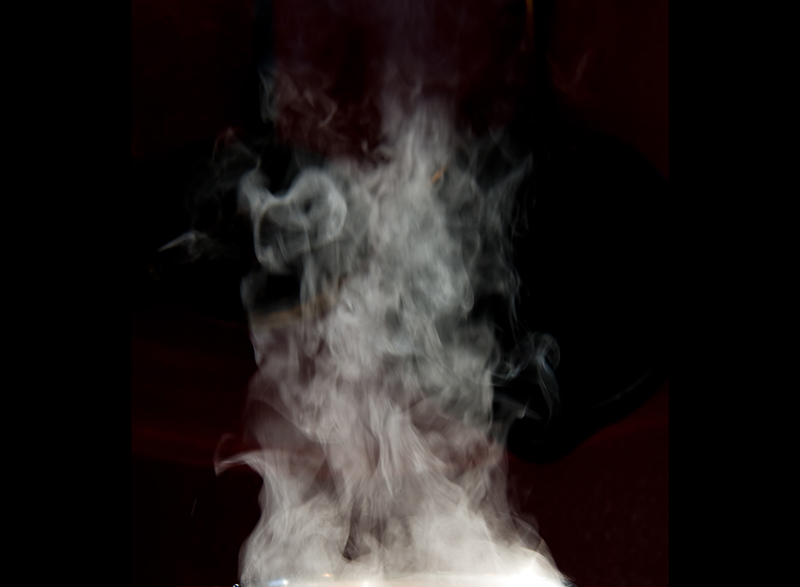
MSS Case June: Two crew members burned by hot water
An incident during a non-routine valve repair led to the sudden release of hot water, severely burning two crew members. Despite safety concerns raised beforehand, the job proceeded without a written procedure in place.
For more Loss Prevention information, please contact:
Joakim Enström, Loss Prevention Officer
E-mail: joakim.enstrom@swedishclub.com
Each month, the Club’s Loss Prevention team issues a new safety scenario to assist members in their efforts to comply with international safety regulations and follow best practices.